Application Success
ROTARY FEEDERS
Make: Shick
Industry: Food & Beverage
Challenge
A facility in the Midwest produces dough that is used in toaster pastries and various cookie mixes. They have numerous rotary feeders to meter the flow of sugar and flour between vessels throughout the facility. These rotary feeders typically run between 5 and 30 rpm. This location was dealing with several issues, including:
- Material leaking through the factory packing to atmosphere, requiring daily housekeeping and resulting in lost product
- Material getting into the bearings and causing premature bearing failure
- Worn rotary valve shafts
Solution
Air purged Inpro/Seal® Bearing Isolators were flange mounted on the rotary feeders to protect against both product leakage and contamination. Inpro/Seal Bearing Isolators are permanent compound labyrinth seals with no wearing parts. These custom engineered seals were designed to run with a 2 to 3 psi air purge to keep the labyrinth between the stator and rotor clear of product.
Result
From 2014 to 2016, the customer replaced 21 Shick rotary valves with the air purged Inpro/Seal Bearing Isolators on both ends of the rotary feeders. The Bearing Isolators have run successfully and maintenance free since installation.
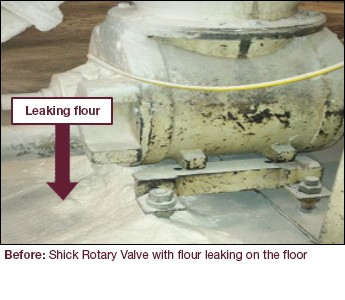
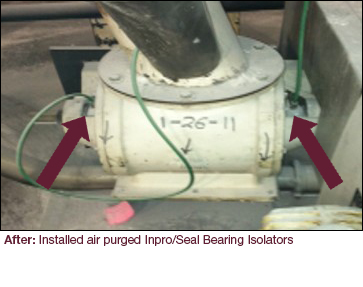
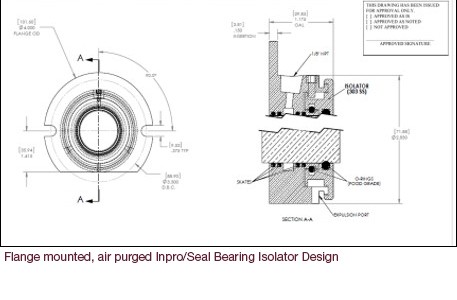
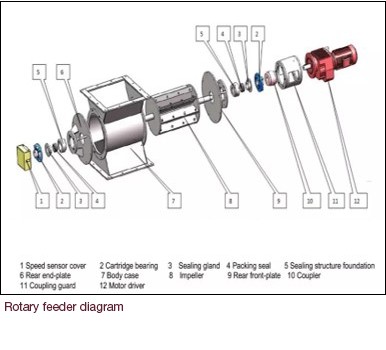
Permanent Bearing Protection
Inpro/Seal Bearing Isolators provide permanent bearing protection against contamination ingress and lubrication loss on rotating equipment. With a unique, non-contacting design, Inpro/Seal Bearing Isolators are maintenance-free and last lifetime of your equipment.
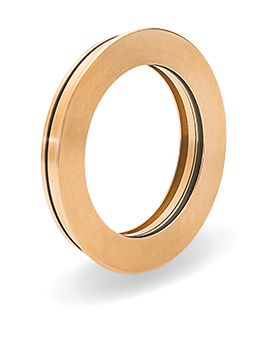
Ready to Get Started?
Count on us to improve reliability and process efficiency within your facility. Our experienced sales and engineering team can design custom engineered bearing protection or shaft sealing solutions to fit the exact requirements of your equipment and operating environment.